How Alcast Company can Save You Time, Stress, and Money.
Wiki Article
The Alcast Company Diaries
Table of ContentsThe 9-Minute Rule for Alcast CompanyNot known Facts About Alcast CompanySome Known Details About Alcast Company The Best Guide To Alcast CompanyWhat Does Alcast Company Do?The smart Trick of Alcast Company That Nobody is Talking About
Chemical Comparison of Cast Aluminum Alloys Silicon promotes castability by lowering the alloy's melting temperature level and improving fluidity during spreading. Furthermore, silicon adds to the alloy's toughness and put on resistance, making it valuable in applications where toughness is crucial, such as automotive components and engine parts.It likewise boosts the machinability of the alloy, making it much easier to process into finished products. In this means, iron contributes to the overall workability of aluminum alloys.
Manganese adds to the stamina of light weight aluminum alloys and improves workability. Magnesium is a light-weight aspect that gives stamina and impact resistance to light weight aluminum alloys.
Our Alcast Company Ideas
Zinc improves the castability of aluminum alloys and assists regulate the solidification process during spreading. It enhances the alloy's stamina and hardness.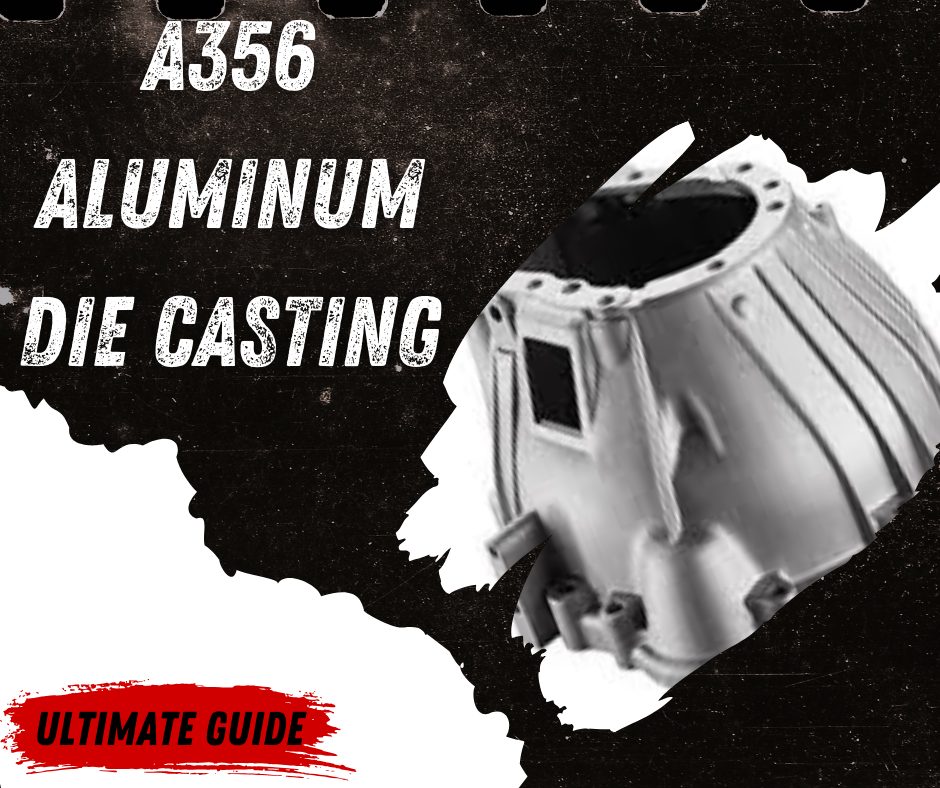
The key thermal conductivity, tensile toughness, yield strength, and prolongation vary. Among the above alloys, A356 has the greatest thermal conductivity, and A380 and ADC12 have the least expensive.
Some Ideas on Alcast Company You Need To Know
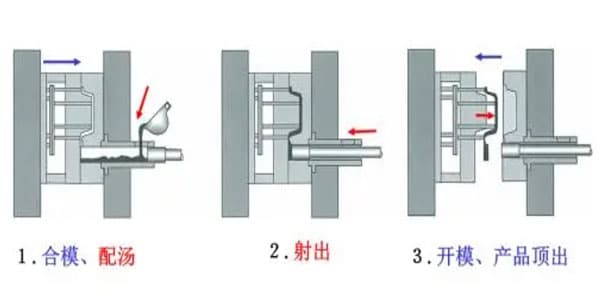
In precision casting, 6063 is well-suited for applications where complex geometries and top quality surface area finishes are critical. Examples consist of telecommunication enclosures, where the alloy's remarkable formability permits sleek and aesthetically pleasing designs while keeping structural stability. In the Illumination Solutions industry, precision-cast 6063 parts create classy and reliable illumination fixtures that require complex shapes and good thermal efficiency.
It results in a better surface coating and better corrosion resistance in A360. The A360 displays superior prolongation, making it perfect for complex and thin-walled components. In precision casting applications, A360 is appropriate for markets such as Customer Electronic Devices, Telecommunication, and Power Tools. Its improved fluidness permits elaborate, high-precision elements like mobile phone cases and communication gadget housings.
The 10-Minute Rule for Alcast Company
Its unique homes make A360 a useful choice for precision casting in these markets, improving product resilience and top quality. Casting Foundry. Aluminum alloy 380, or A380, is an extensively utilized casting alloy with several distinctive attributes.
In accuracy spreading, light weight aluminum 413 beams in the Customer Electronic Devices and Power Equipment industries. This alloy's superior rust resistance makes it a superb selection for outdoor applications, making certain long-lasting, resilient products in the stated markets.
The 3-Minute Rule for Alcast Company
The aluminum alloy you choose will significantly influence both the casting process and the properties of the last product. Because of this, you have to make your decision carefully and take an informed approach.Determining one of the most suitable light weight aluminum alloy for your application will suggest considering a wide selection of characteristics. These relative alloy features comply with the North American Die Casting Association's standards, and we've separated them into two classifications. The very first classification addresses alloy characteristics that impact the production process. The second covers attributes impacting the buildings of the end product.
3 Easy Facts About Alcast Company Explained
The alloy you choose for die casting directly influences several elements of the casting go to these guys procedure, like how easy the alloy is to collaborate with and if it is prone to casting problems. Warm cracking, additionally referred to as solidification breaking, is a regular die spreading flaw for aluminum alloys that can result in inner or surface-level splits or cracks.Particular aluminum alloys are a lot more at risk to hot breaking than others, and your choice ought to consider this. One more usual problem located in the die casting of light weight aluminum is die soldering, which is when the actors stays with the die wall surfaces and makes ejection challenging. It can damage both the cast and the die, so you need to search for alloys with high anti-soldering buildings.
Rust resistance, which is already a remarkable characteristic of light weight aluminum, can vary substantially from alloy to alloy and is an important particular to consider depending upon the environmental conditions your item will be subjected to (aluminum foundry). Use resistance is an additional property typically looked for in aluminum products and can separate some alloys
Report this wiki page